Internships
GearHeads
2015 - May
This was first experience working on professional product design that I had. While interning for them, I sat in on and contributed to client and design meetings. I got to be a part of the design process for a unique gambling table, as well as a novel medical device to improve post-op surgical patient outcomes.
My experience at GearHeads was an eye-opening one. At just 18, I got to see the day to day work of engineers and designers developing innovative products. Working with them helped cement my interest in engineering and design. I still believe that a long term goal of mine is to end up working at a place like this.

NVTS (Night Vision Technology Solutions)
2018 - July
My first professional internship since I began studying engineering was with NVTS. They're a little company in Rhode Island that does amazing work. After three years of slogging through engineering curriculum, I was growing weary of the path that I had chosen. Working with NVTS couldn't have come at a better time, the people I worked with, and the projects that I helped on genuinely renewed my interest in my career path. I couldn't have asked for a better group to spend a month working with.
I spent a lot of my time helping with design on Solidworks, but also worked with another engineer to overcome countless hurdles; such as bore sighting, thermal management, and sealing an enclosure.

NOAA-ESRL
2019 - June through December
This internship started as a continuation of my senior design project through CU boulder. When the project ended, the platform was in a presentation ready state, I was hired on to continue the team's work and get the motion compensation platform deployment ready. I also assisted with the installation of the group's MD2 custom Lidar unit into a research aircraft for the FireX-AQ field campaign. My project/ internship ended with the installation of the motion compensation platform on the NOAA vessel Ronald Brown for its deployment on the ATOMIC mission.
My time with NOAA was very enjoyable and involved a large variety of work. The Atmospheric Remote Sensing Group that I worked with focused in large part on the use of Lidar to gather atmospheric and oceanic data. My coworkers in this group used Lidar systems to study everything from fish counts to ozone production to wind fields. The main instrumentation work that I got to witness was for their Micro Doppler systems, in which they miniaturized a doppler lidar for tracking atmospheric aerosols.
My motion compensation platform was designed for deployment on the ATOMIC field campaign on the USS Ronald Brown. It will spend two and a half months in the Caribbean and Atlantic, compensating for the motion of the ship so that the Lidar unit mounted on it can gather meaningful data.
One of my main tasks this summer has been PID tuning to improve the performance of the platform, and to develop tuning procedures for optimal disturbance rejection as conditions at sea vary. I tested the system performance by adding a sine into the feedback loop and calculated RMS, MAE and peak error as the system tried to track the artificial disturbance.
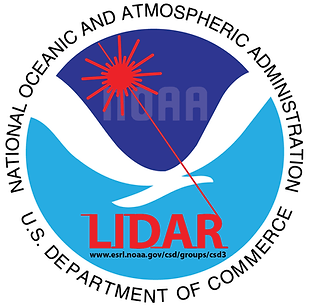.png)
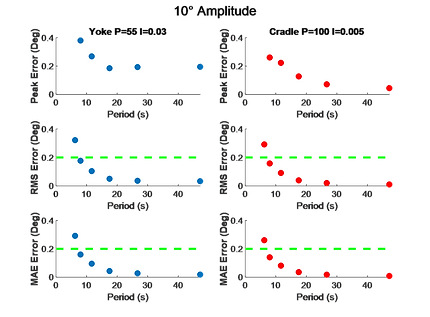

Above are some plots looking at performance bandwidth (left) and relationships between performance and various tuning parameters (right). These plots show a small portion of the data that I gathered to test the system. My goals were (1) to prove tune-ability of the system (2) to identify baseline, high performing tuning parameters and (3) develop process change procedures for disturbance rejection given different frequencies and amplitudes of ship motion. Although my tests could not accurately simulate heave, the impacts of wind and other unknown disturbances that might be seen on the ship, I was able to answer each of the questions, which will inform changes made on the ship in December.
Another one of my tasks when preparing the system for deployment was LabVIEW debugging and addition of safety features. When I restarted work in June (at NOAA rather than CU Boulder) the safety features were not setup properly and the code was disorganized and could not run for longer than 2 hours before crashing. This was a big issue when the system needs to be operated for months at a time with minimal babysitting. For safety features, I installed and wired limit switches and integrated them into the motor driver software, as well as improved E-stop button function. I also added engaged and error warning lights to the exterior of the electronics enclosure. In the LabVIEW code, I found numerous memory leaks which were causing issues with system performance, reduced sensor reading and motor command latency and located and fixed the issue causing periodic crashes (.NET disconnect error). In the LabVIEW code, I also made the large code more modular by breaking important functions into sub Vi's.
Overall, my work involved LabVIEW and Matlab programming, electrical wiring, machining and a huge amount of mechanical tweaking to get the system running. I got to see a complex project with nearly 300 components go from concept to deployment in less than a year and a half. Along the way I had some incredible learning experiences and got to work with some amazing people. Below is a photo gallery showing some of the work that I got to be a part of, including installing equipment in a research airplane, and even flying cross country to install the system onto a NOAA research ship.
As an update, the ATOMIC mission finished in February and the system preformed phenomenally. The system was correcting within 0.05 degrees RMS even in heavy seas. I'm really glad that it held up to the abuse of the high seas and will eventually be used on a truck for studying pollutants around the Washington DC area.